Overview
The Environmental Monitoring System (EMS) is an all-in-one solution for monitoring underground mining conditions. Mounted within a Drive, Decline or Return Airway. The system will monitor atmospheric conditions and relay in real time what is happening
The problem
The underground mining environment is undoubtedly harsh and expensive to operate. Confined spaces, minimal ventilation and underground vehicle emissions can compromise air quality underground. Underground blasting is an essential part of the mining process but results in an abundance of toxic gases being released into the enclosed environment.
Re-entry into blast fume-affected underground areas is a safety and productivity concern for most mines. Lengthy re-entry times may improve clearance of noxious gases but can result in production delays and decreased overall productivity. Re-entry times into development headings are often standardized based on worst-case scenarios, resulting in unnecessary delays. Fume clearance from blast areas can be mathematically estimated using a number of different methods however a complicating factor of fume clearance is considering the volume, efficiency, and discharge location of fresh air ducts required to clear development blast areas.
The two most dangerous gases in an underground mine are nitrogen oxide, generated from explosive blasting, and carbon monoxide, from trucks and other mining equipment using internal combustion engines. These gases are crucial to monitor to prevent any worker from being in a toxic environment.
Following a blast there is a minimum wait time before re-entry is permitted. This is a time of minimal productivity, and where possible should try to be reduced. When there is no active feedback on live gas readings meaning that workers may be waiting for an unnecessary time, or a worst-case scenario of sending people (re-entry crew) into an unsafe environment.
Blasting with explosives is an essential activity for developing tunnels in most underground hard rock mines, however, the process introduces a number of hazards that must be controlled to ensure a safe work environment. A major consideration is the release and removal of noxious gases from the mine before the re-entry of workers to areas that may be affected by blasting fumes. Traditional methods of estimating blast fume dispersal can provide accurate indications of clearance times if carefully calibrated to mine conditions; however, these tools are rarely used systematically with blasting activities due to the wide range of variations in ventilation and blasting conditions. In addition, the traditional calculation methods provide a limited platform for calculating mine-wide fume dispersal, where mixing of airflows and dilution limit the use of fume concentration calculations. Risks associated with underground gas levels are:
- Placing re-entry crews at risk if the gases are still unsafe following a blast.
- Exposure to bogging crews when they are bogging (releasing pockets of gas).
- Exposure to diesel particulates through inadequately ventilated environments and diesel equipment operated within confined environments.
How EMS solves the problem
Digital Terrain offers an advanced Environmental Monitoring system that facilitates real-time air quality monitoring to allow faster re-entries, Visibility of environmental conditions within the mine to forewarn re-entry crews prior to being exposed to an unsafe environment and greater productivity by potentially reducing nonproductive face time. Digital Terrains EMS detects and monitors toxic and flammable gases in underground mining operations from the surface to enable safe entry for personnel following blasting in an underground mine.
Digital Terrain recognises the need to bring all the sensor information back into a central on prem application that applies a visual representation to the data and through the software enables a control room or Shift boss the ability to control a devise within the underground mine.
See Figure 1: Gas Sensor Chart
See Figure 2: EMS unit view from control room on site
Digital Terrain EMS units are capable of measuring 8 gases, wet and dry bulb, air velocity, dust particulate, and humidity. Environmental readings can be viewed from the surface in our customised real-time dashboards.
Printable Brochure (PDF)
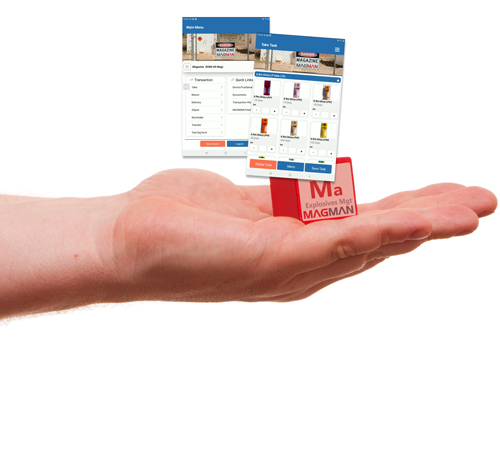
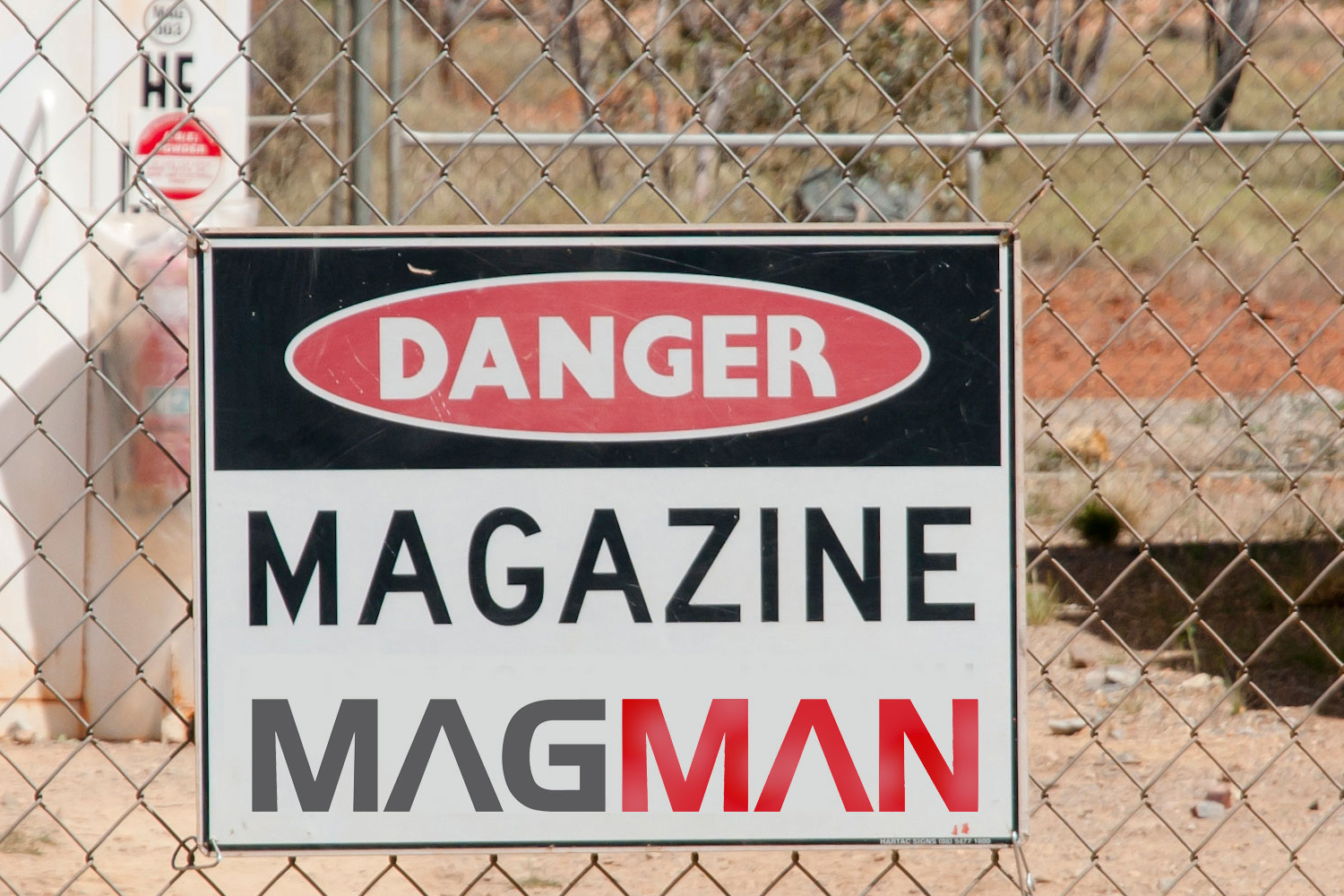
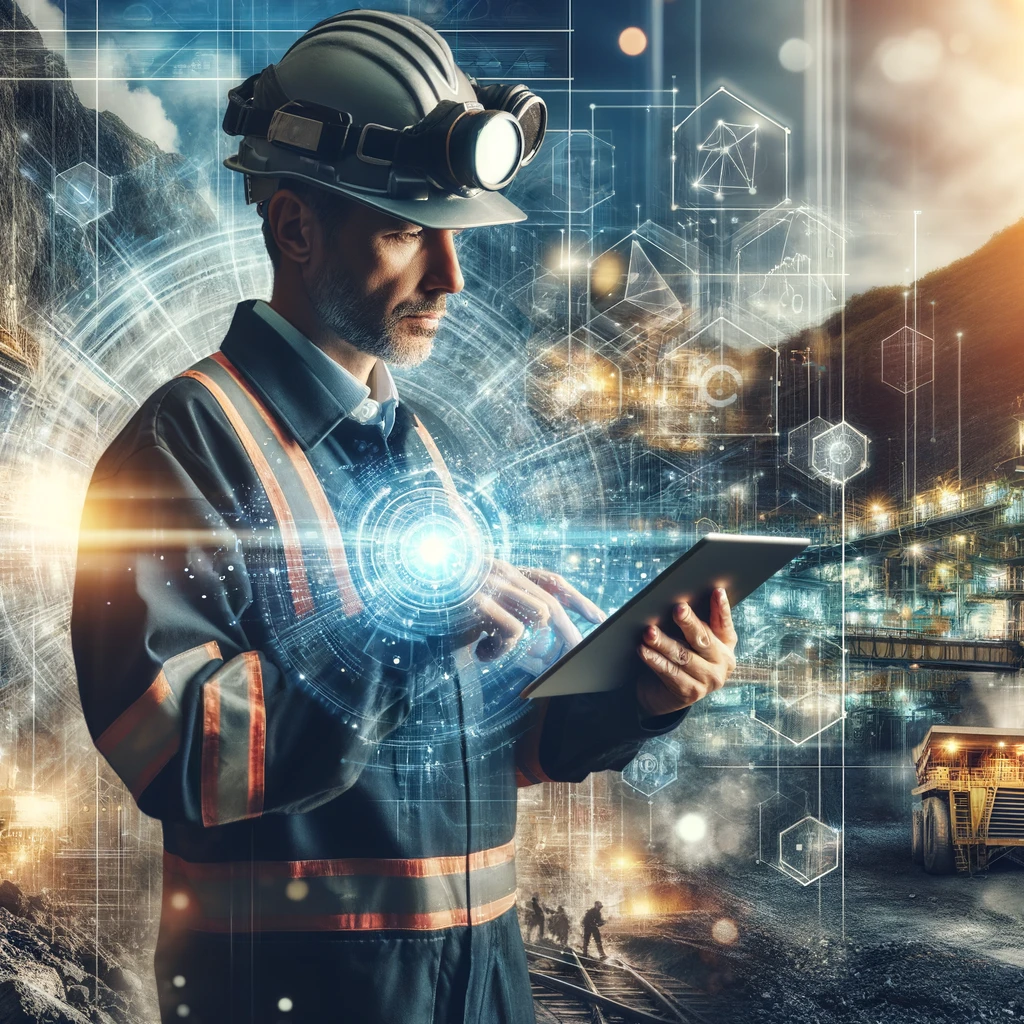
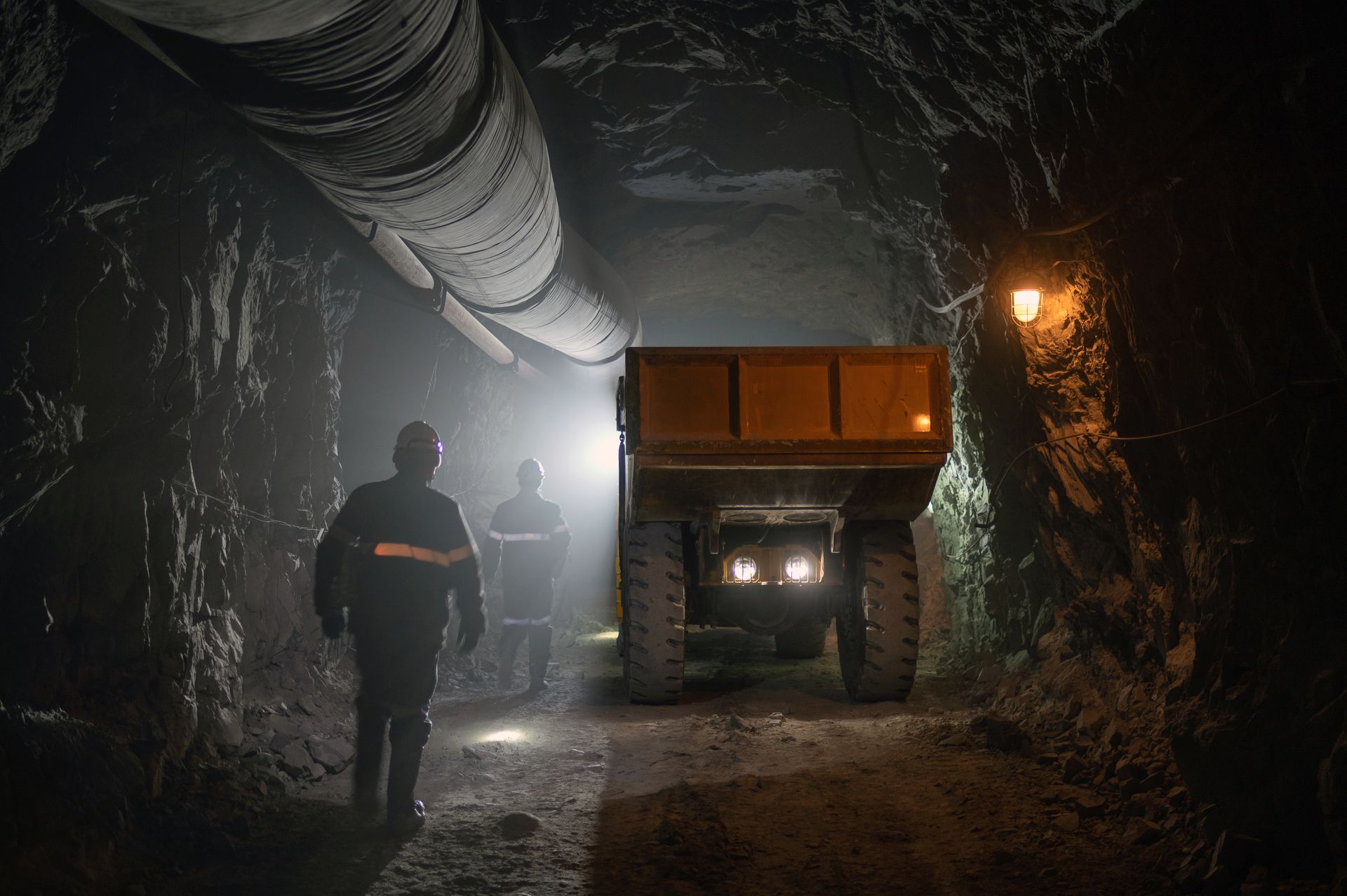
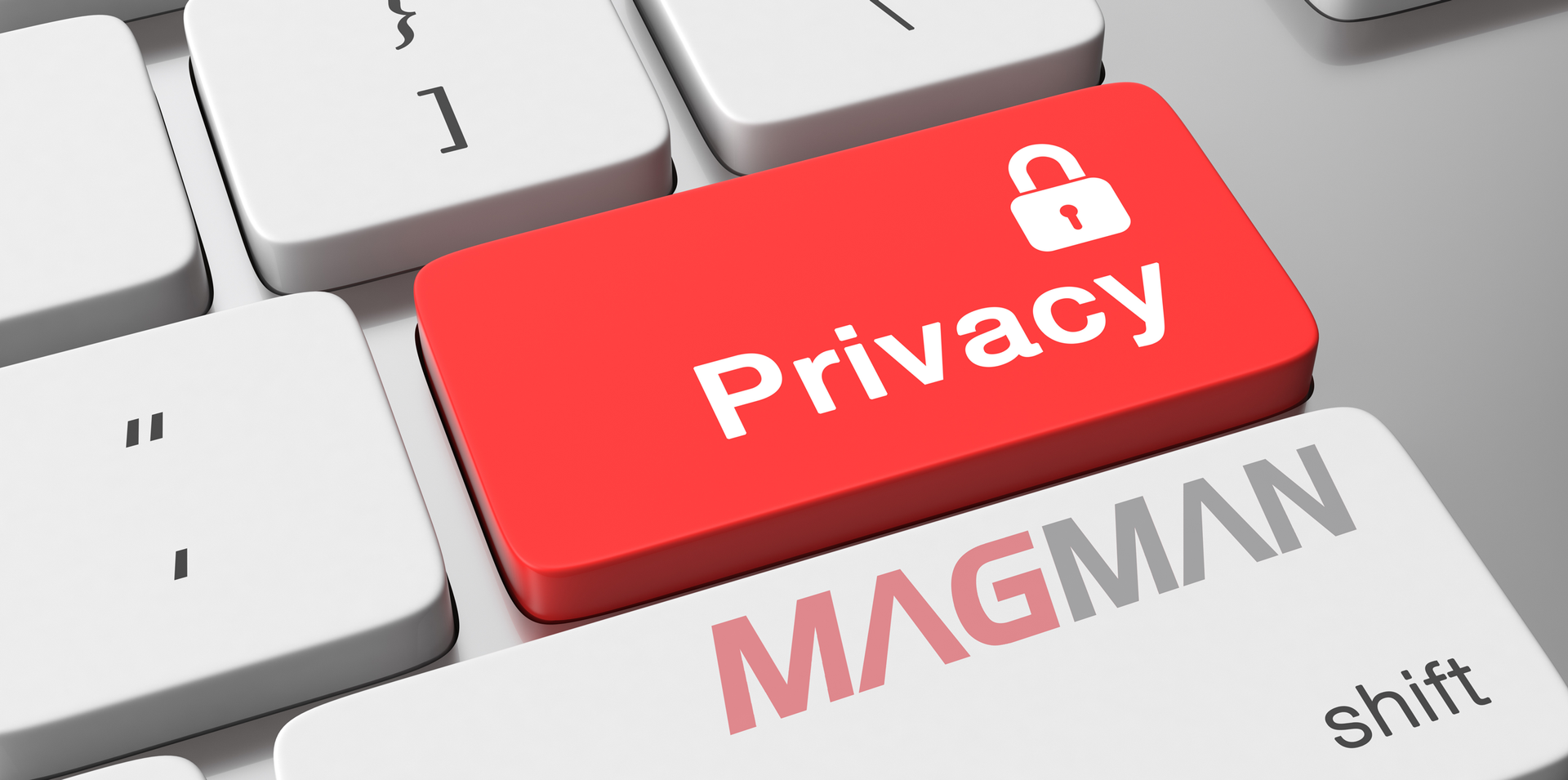